Pressure vessels, drums, funnels & special designs made of stainless steel for pharmaceuticals, cosmetics & fine chemicals that set new standards
Sicherheit & Reinheit in Produktion, Transport & Lagerung erhöhen durch minimale Partikelanhaftung
- Contamination-free production: Stainless steel surfaces from BOLZ INTEC are optimized for industries with the highest demands on hygiene and cleanliness.
- Reproducible product quality: Stainless steel surfaces from BOLZ INTEC are flawless and reduce the risk of production downtime & product recalls.
- Compliance with the highest standards: Stainless steel surfaces from BOLZ INTEC guarantee compliance with GMP and EHEDG standards.
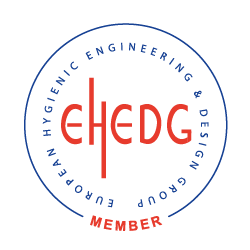
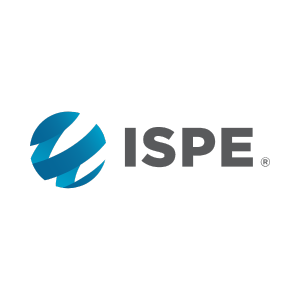
Over 2,000 customers in 48 countries place their trust in our stainless steel containers, drums & appliances
BOLZ INTEC GmbH steht für Innovation, Qualität und Präzision in der Herstellung von Edelstahlfässern, Druckbehältern, Apparaten und Sonderkonstruktionen nach den Spezifikationen unserer Kunden in Branchen mit hohen Qualitätsansprüchen.
Als langjähriger Partner der Pharma-, Kosmetik- und Feinchemieindustrie schaffen wir Lösungen, die Maßstäbe bei Qualität und Effizienz setzen, die unseren Kunden signifikante wirtschaftliche Vorteile bringen und die die Sicherheit und Reinheit von Produkt und Produktion erhöhen.
Unsere Edelstahlbehälter und Sonderkonstruktionen werden nach GMP und EHEDG Hygienic Design Richtlinien gefertigt. Sie sind prädestiniert für den Einsatz in hygienesensiblen Umgebungen. Die praxis- und kundennahe Produktentwicklung von BOLZ INTEC GmbH gewährleistet kompromisslose Qualität und Sicherheit.
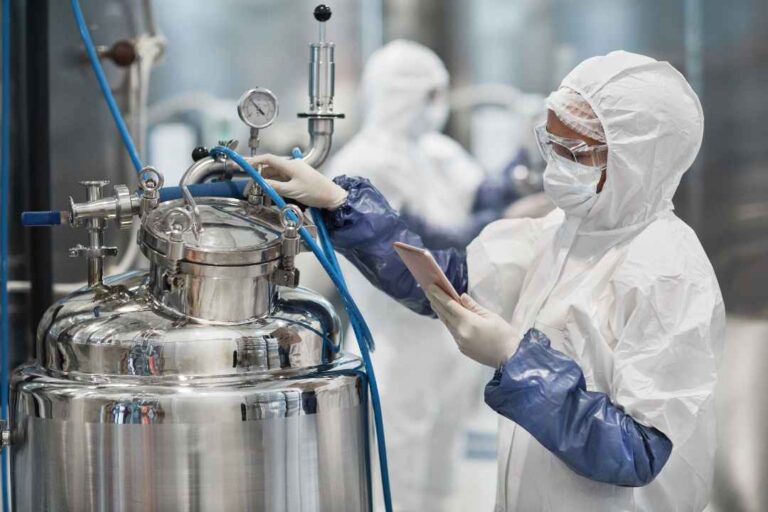
15 of the 20 largest pharmaceutical companies worldwide are customers of BOLZ INTEC
15 der 20 größten Pharmaunternehmen weltweit zählen zu den Kunden von BOLZ INTEC GmbH
Market capitalization of the top 20 pharmaceutical companies in 2022, source: GlobalData
Kunden aus diesen Branchen erhöhen ihre Effizienz mit Behältern, Apparaten & Konstruktionen aus Edelstahl von BOLZ INTEC GmbH
Product portfolio of BOLZ INTEC
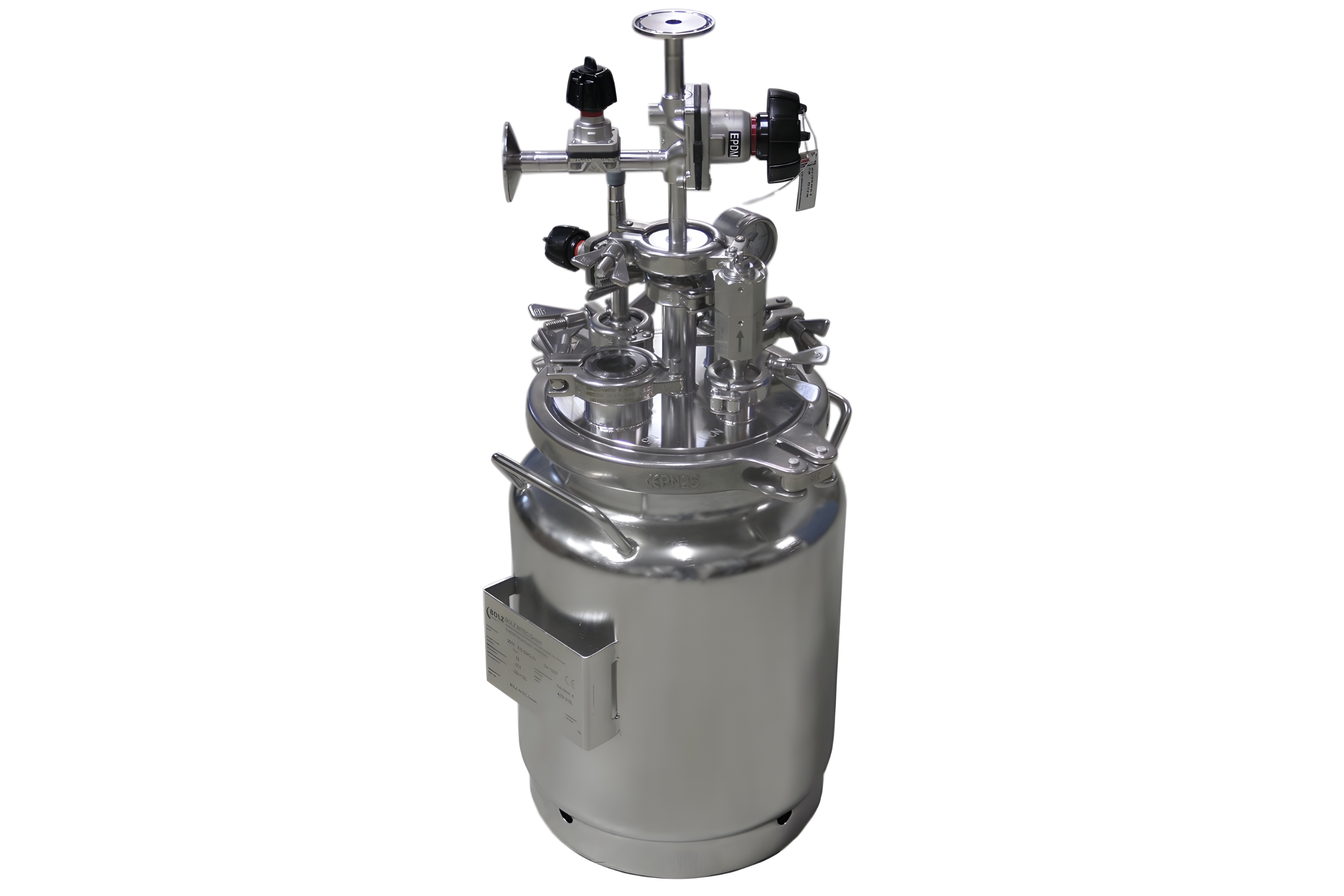
Pressure vessel
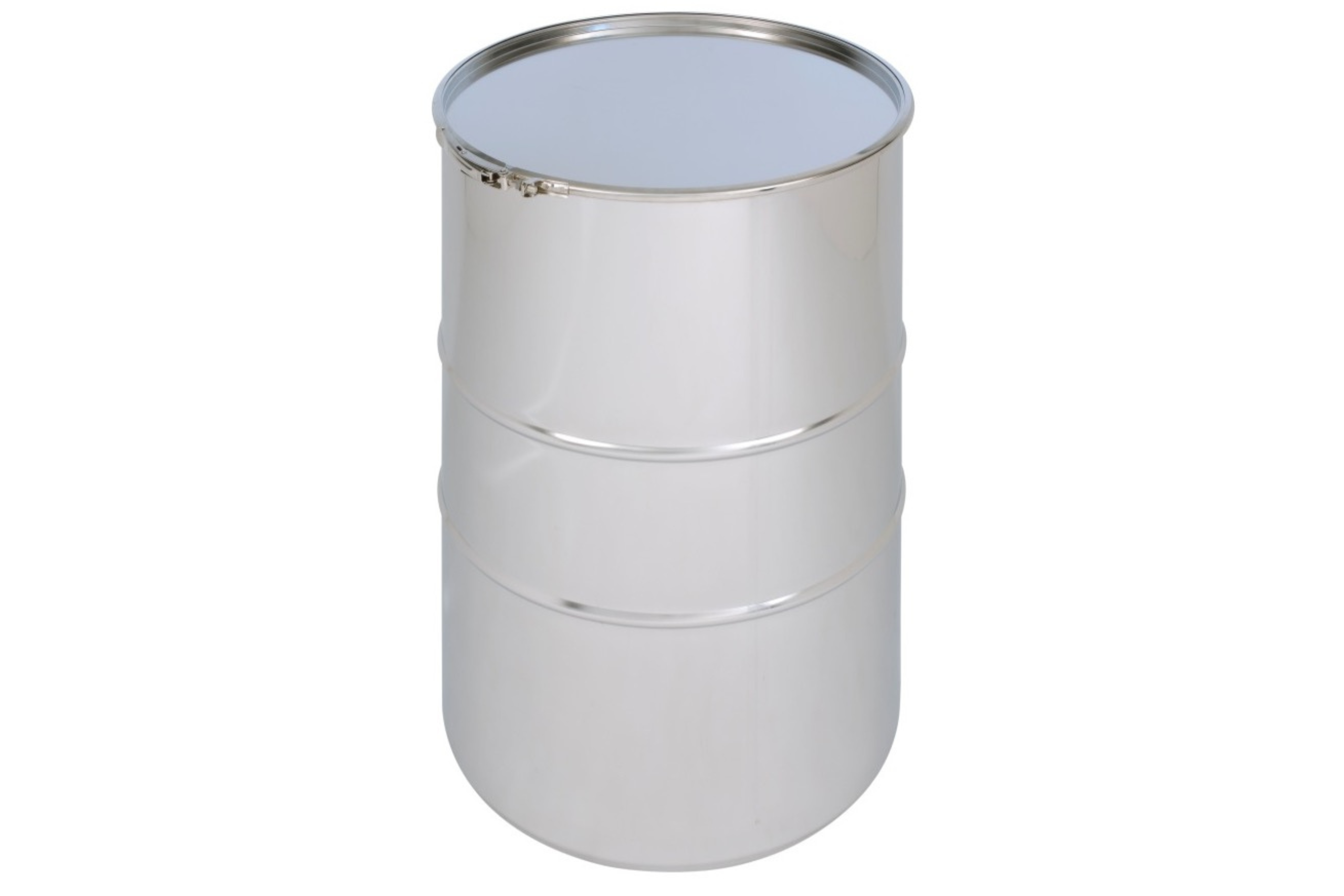
Stainless steel drums
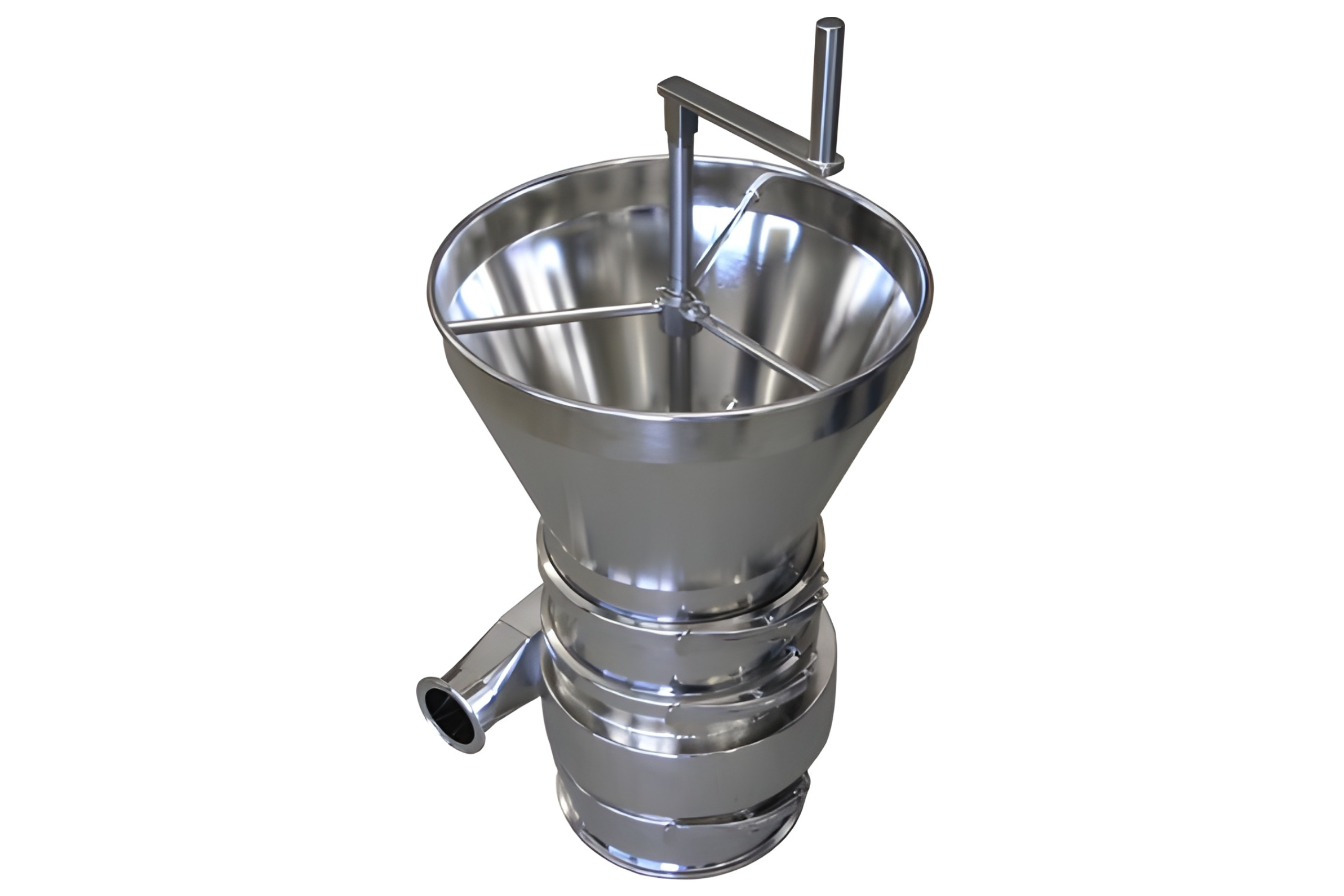
Funnels & special funnels
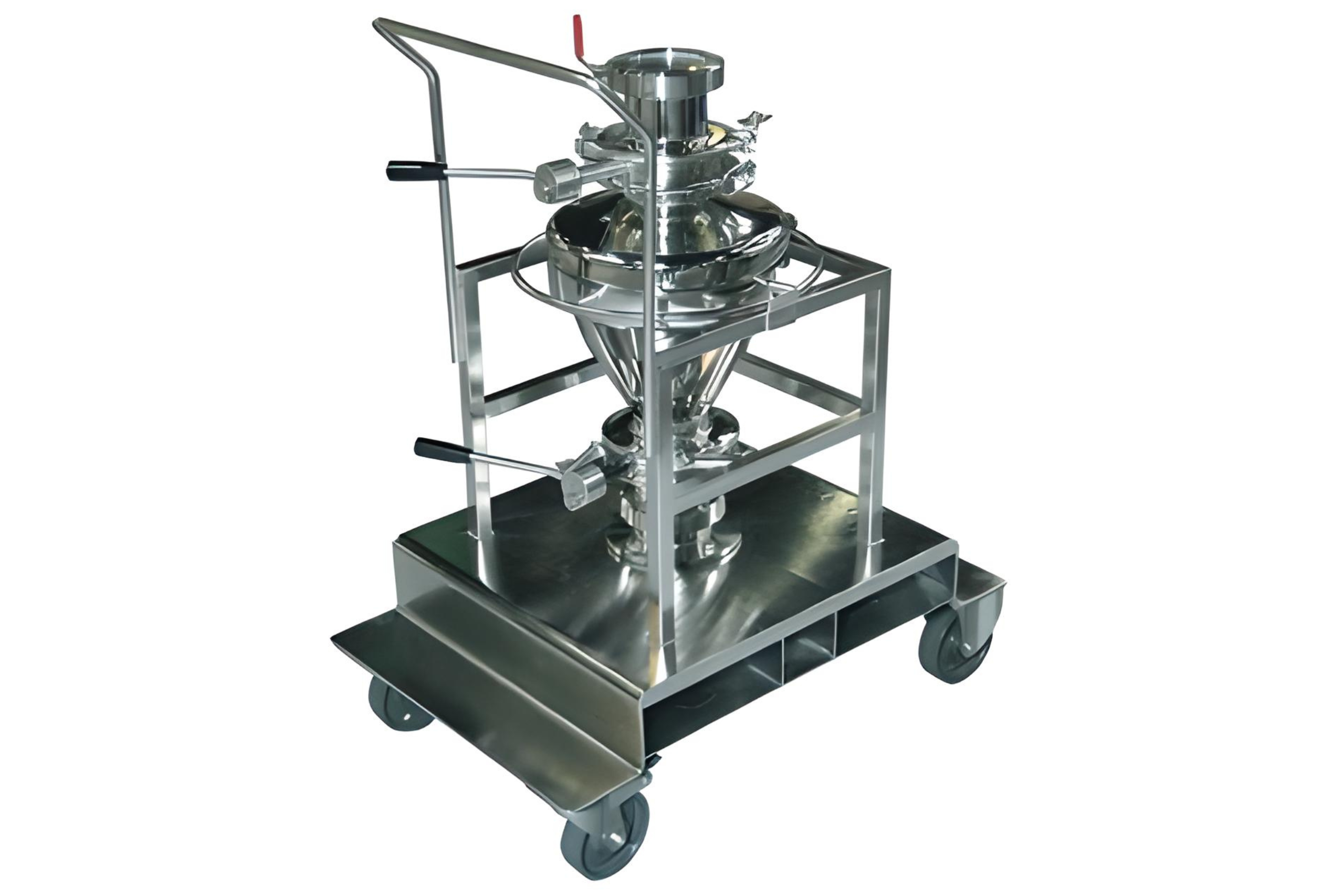
Special constructions
The Optimized Grind Finishing® process (OGF)
In the pharmaceutical, chemical and food processing industries, minimizing build-up in containers is a critical factor for efficiency and quality. The build-up of substances on the inside walls of containers can lead to increased cleaning effort, product losses and contamination. This costs money and ties up resources. Especially in industries where EHEDG (European Hygienic Engineering & Design Group) certification and hygienic design are becoming increasingly important, minimizing adhesion has become a critical factor.
Research carried out by BOLZ INTEC in cooperation with the University of Constance has shown that the way in which stainless steel surfaces are removed plays a key role in minimizing adhesion. Different grinding methods result in different adhesion behavior, despite the same Ra values, and the OGF process from BOLZ INTEC leads to a lower adhesion of particles.
Below is a scanning electron microscope image of the stainless steel surface after electropolishing and Optimized Grind Finishing, as well as images of the surface texture roughness data and repeatability.
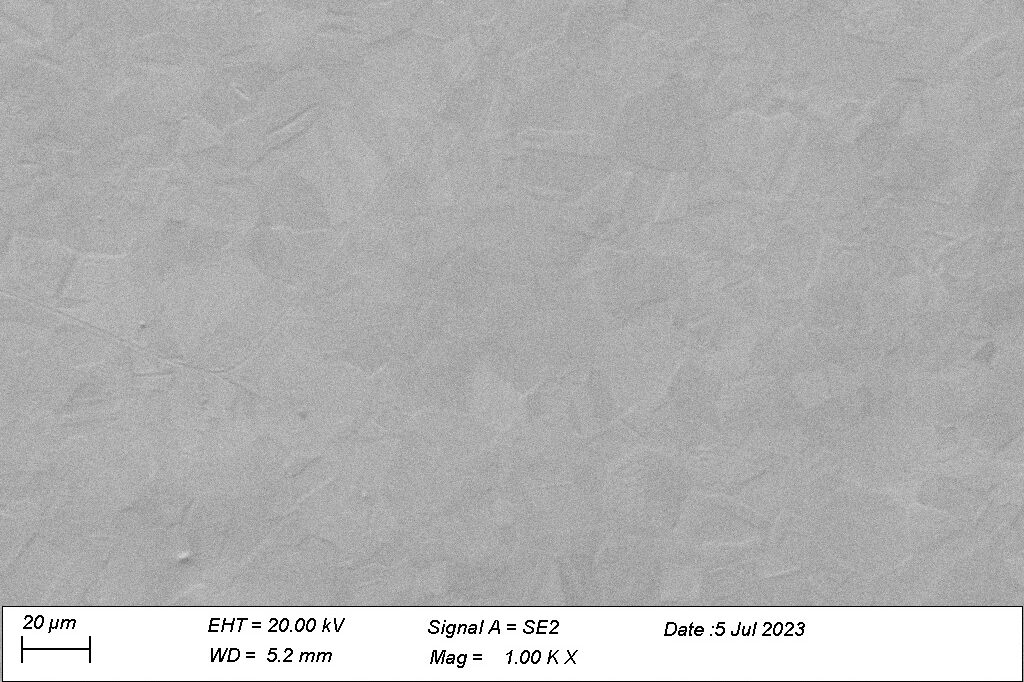
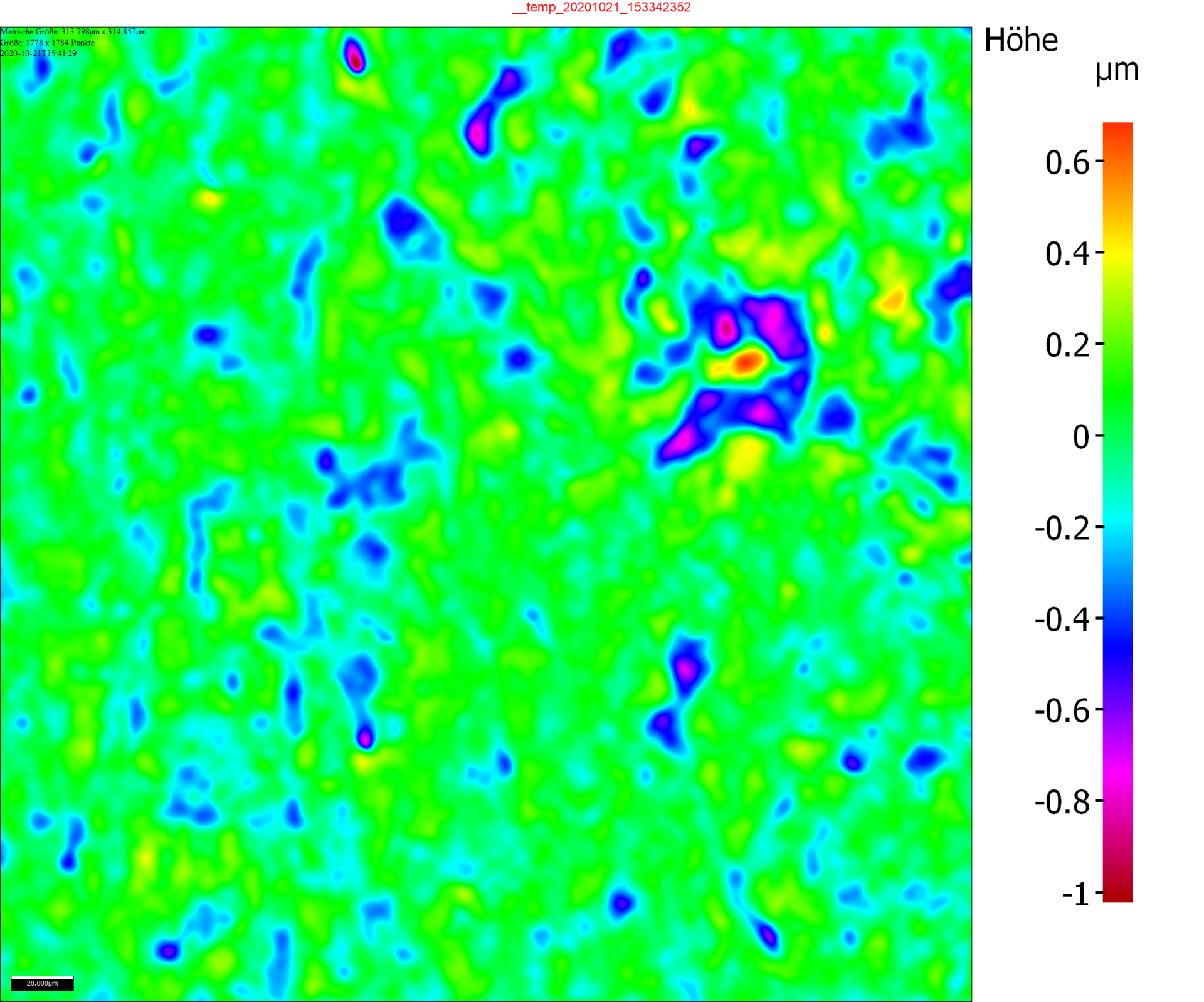
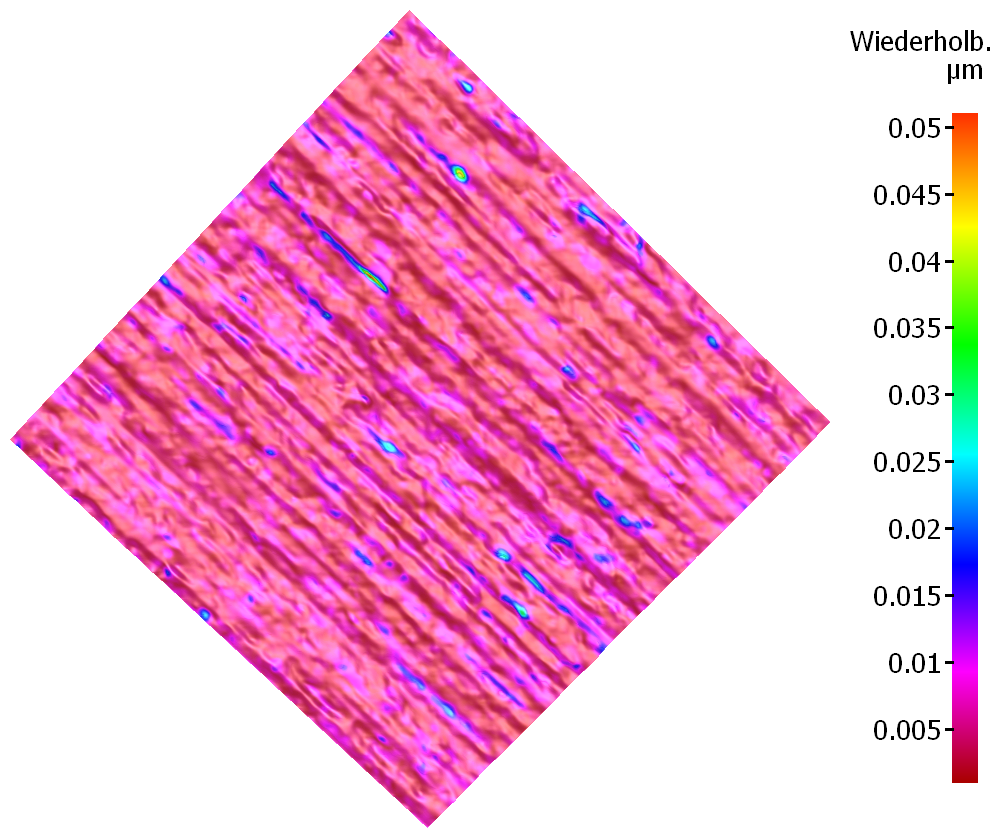
Easy cleaning & minimal adhesion
The Optimized Grind Finishing (OGF) process leads to a low adhesion of particles on the surfaces of the containers. This significantly improves cleaning efficiency and reduces the risk of contamination of product batches.
Reproducible surface quality
The OGF process enables reproducible surface quality. In contrast to conventional processes, in which variable factors such as manual contact pressure or the quality of abrasives play a role, the OGF process offers consistent surface quality.
Visual aesthetics and low number of errors
The stainless steel surfaces treated with the OGF process have an attractive appearance and defects in the surface structure are significantly reduced thanks to the fine and gentle removal process. This is particularly important in industries that place high demands on safety.
Improved corrosion protection
The electropolishing process not only improves the optical quality, but also results in chemical changes that lead to improved corrosion protection. This is particularly relevant for applications in chemical and pharmaceutical processes.
Reduced risk of batch contamination
The improvement in cleaning behavior through the OGF process leads to a significant reduction in residual dirt adhesion in the containers. This significantly reduces the risk of contamination between different product batches.
Applicability in critical industries
The process is seen as particularly advantageous for critical industries such as nanotechnology or biotechnology and pharmaceutical technology, where the highest purity requirements and the avoidance of contamination are of crucial importance.
Increased efficiency through minimal adhesion
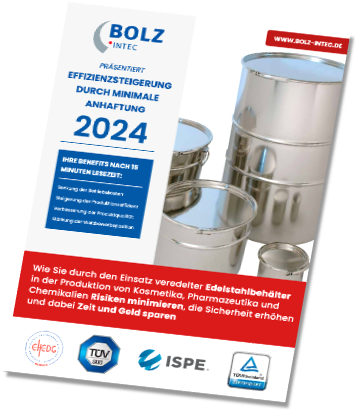
Simply send an e-mail and receive the download link
Services from BOLZ INTEC
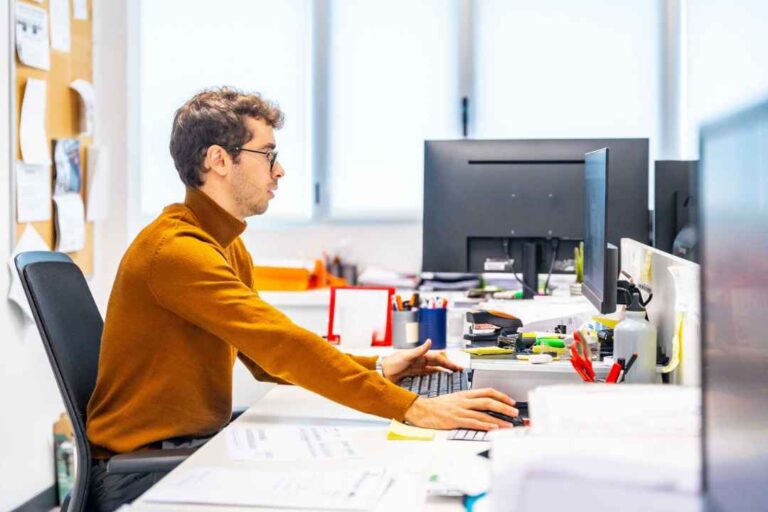
Technical advice & design
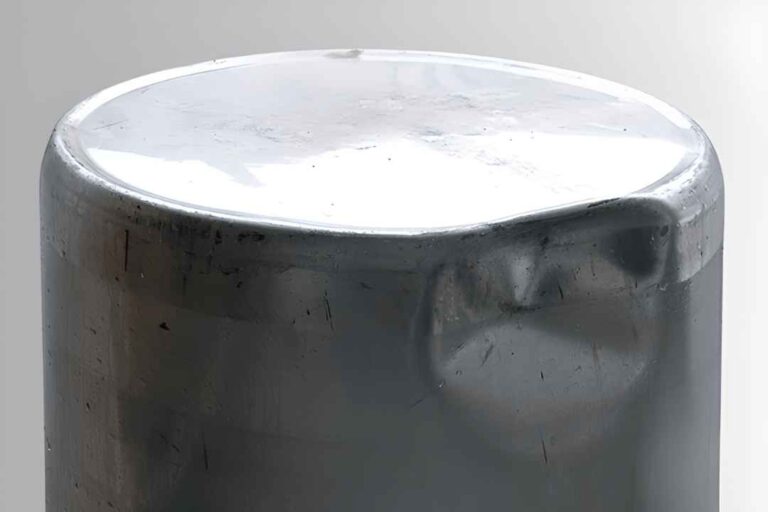
Barrel repair
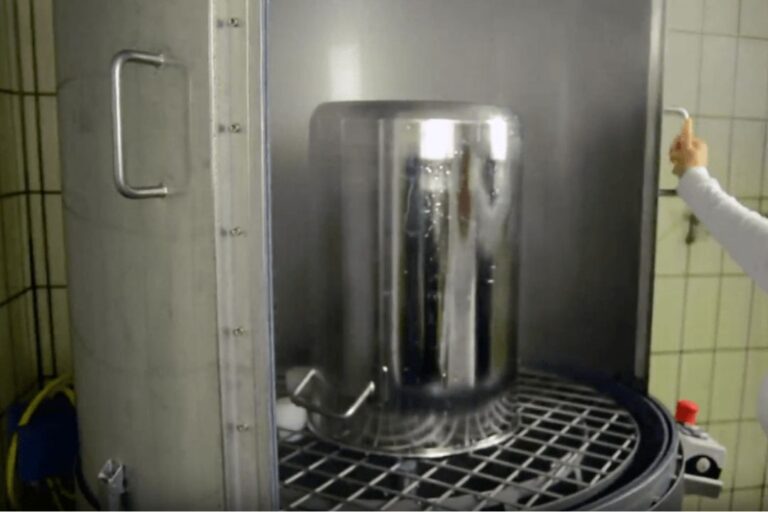
Simoflex® drum wash
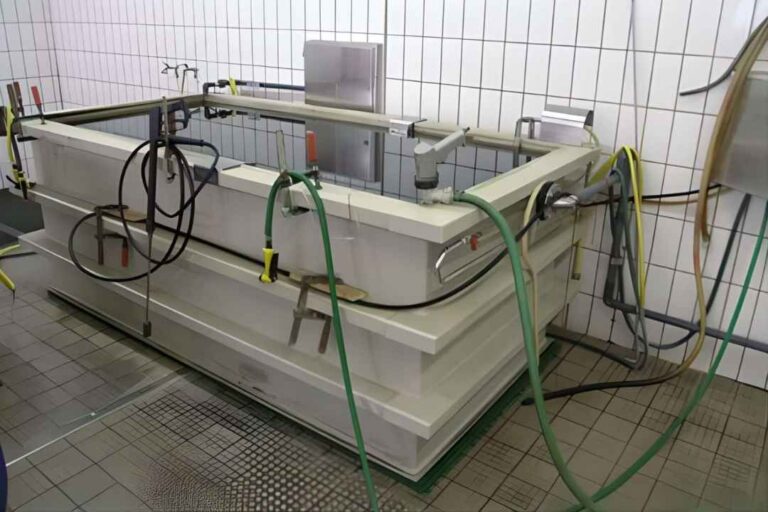
Electropolishing
Why customers around the world choose our stainless steel containers
Tradition & innovation since 1919
BOLZ INTEC specializes in the manufacture of stainless steel drums, pressure vessels, agitator vessels, transport containers and transfer systems for hygiene-sensitive industries.
High vertical integration
BOLZ INTEC has acquired outstanding expertise in the machining of stainless steels and special materials such as Hastelloy. Combined with the skills and abilities of our team, this enables us to achieve maximum vertical integration. All production steps are carried out in-house. BOLZ INTEC is therefore able to react extremely flexibly to customer delivery date requests and guarantee unique quality.
Customized solutions
Our design department designs, plans and develops practical products according to our customers' requirements. These include, for example, containers for pasty substances or liquids, transport containers for UN hazardous goods, cans for the storage and transfer of active ingredients, suction hoods for dust-free container loading and much more.
One-off production & small series
BOLZ INTEC also manufactures custom-made products and small series.
Machines for perfect surfaces
Nothing in the BOLZ INTEC machine park is off the shelf. From the deep-drawing press to the electropolishing system, we work with special machines that have been developed according to our own specifications in order to meet the highest standards of quality and precision.
Traceability & reproducibility
BOLZ INTEC's QM system and our intensive testing procedures ensure the consistent quality of the stainless steel surfaces manufactured by BOLZ INTEC. In this way, we make a decisive contribution to the traceability of products in critical industries.
Trust & security
Our striving for perfect quality, state-of-the-art production methods, but also craftsmanship and know-how are the basis for the superior BOLZ INTEC quality, which means safety and reliability for our customers. It is therefore not surprising that 80% of our customers have reordered every year for the last 10 years.
Comprehensive certification
We regularly have our quality certified externally: DIN 9001:2015, DIN EN ISO 3834-2:2006-03, DIN EN ISO 115085-2/CL1. We are a specialist company according to WHG §19/1 and carry out process tests according to DIN EN ISO 15614-1, operator tests according to DIN EN 1418. BOLZ INTEC fulfills the Pressure Equipment Directive-2014-68-EU/AD-2000 HPO and employs Intern. Welding engineers (DVS/IIW 1170).
High efficiency, low costs & great economy thanks to superior stainless steel surfaces
Time savings in production
The use of stainless steel containers with optimized surfaces leads to significant time savings in the production process. By minimizing the build-up of materials, cleaning and maintenance times can be drastically reduced. This enables the containers to be reused more quickly and increases the overall efficiency of the production lines. In a production-intensive environment where time equals money, this time saving represents a significant economic advantage.
Reduced risk of production downtime
The reproducible quality of the stainless steel surfaces and the reduced number of defects minimize the risk of production downtime due to surface problems. This can lead to higher overall productivity and less downtime.
Reduction of production losses
Optimizing the container surfaces also minimizes the amount of product loss. Reduced adhesion means that more of the material produced is available for its intended use and does not end up as waste. This is a particularly important factor in industries where high-quality or very expensive materials are processed.
Improvement of product quality & product safety
Contamination-free production results in a higher quality end product. This is crucial in industries with strict quality and purity requirements, such as pharmaceuticals and food production, where purity and safety are top priorities. The use of optimized stainless steel containers can therefore also lead to an improvement in brand image and customer satisfaction.
Cost savings through more efficient cleaning
In addition to saving time, optimized surfaces also lead to a reduction in the costs of cleaning processes. Less build-up means less need for cleaning agents, water and energy. There is also less wear and tear on the containers themselves, which increases their service life and reduces the need for new purchases. In the long term, these savings in operating costs can make a significant difference to a company's profitability.
Longer container service life
The improved corrosion protection provided by the electropolishing process helps to extend the service life of stainless steel containers. Customers can thus reduce their costs for replacement investments and maintenance.
Reach your goal in just a few steps
Request
Send us an e-mail, give us a call or book an appointment via Calendly. In a phone call with one of our competent contacts, we will clarify a few questions in advance using checklists and send you a non-disclosure agreement (NDA).
Test phase
Based on your objectives and specifications, you will receive drums, containers, funnels and accessories from our test center - as required - to try out and test. You can use your test equipment to verify or adapt the specifications of your request.
Offer
During a visit to your premises, our competent contact partners will advise you on clarifying any final questions, finding solutions to identified problems and defining your exact requirements. We can then start production.
The last barrel arrived last week. We received all the parts we ordered on time. Your prompt and professional support enabled us to keep to our schedule. Finally, I would like to thank you for your constructive, professional and reliable cooperation."
the customer has accepted the funnel and is very satisfied.
I wanted to thank you again for the fast processing and delivery..."
Thank you very much for this good news and please pass on our thanks to your production staff and all those involved, as it has now been possible to produce the tanks for us at very short notice. You have helped us a great deal."
Our project team looks forward to your inquiry
Do you have questions about our products and services or would you like advice from one of our competent employees?
Give us a call or send us an e-mail. We will make time for you and will be happy to call you back if you wish.
Interesting & worth knowing
1919
is the year in which BOLZ INTEC was founded
49
BOLZ INTEC has highly qualified employees with a passion for quality.
0,5
liters is the smallest drum in the world from BOLZ INTEC with the dimensions Ø120 V0.5l
20
years is the service life of a stainless steel drum from BOLZ INTEC with regular maintenance
3
mal schneller ist die Fließgeschwindigkeit viskoser Medien in einem Fass von BOLZ INTEC mit Optimized Grind Finishing®
4
ist der Faktor der Zeitersparnis bei der Reinigung von Edelstahlfässern mit Veredelung durch das Optimized Grind Finishing® (OGF)-Verfahren von BOLZ INTEC
4
mal geringer ist die Anhaftung sehr feiner Pulver (15-25 µ) an Oberflächen von BOLZ INTEC mit Optimized Grind Finishing®
1963
BOLZ INTEC started with the production of round containers made of stainless steel
3.500
m2 is the production area of BOLZ INTEC
12
bar is the maximum pressure for pressure vessels from BOLZ INTEC
500
liters is the capacity of BOLZ INTEC's largest drum
0,05
Ra < 0.05 µm is the roughness of stainless steel surfaces that have been refined using the OGF process from BOLZ INTEC
News / Press articles / Dates / Trade fairs
Nichtrostenden Stahl schonend bearbeiten – maschinenbau 3|2025
Nichtrostenden Stahl oberflächenschonend schleifen
Neues Schleifverfahren sorgt für hygienische Perfektion
Become our development partner or sales partner!
Contribute your expertise and all your experience to achieve common goals and realize innovative ideas.
- Entwickeln und gestalten Sie in enger Zusammenarbeit mit BOLZ INTEC GmbH branchenführende Produkte, Services und Projekte.
- Bieten Sie die innovativen und umsatzstarken Produkte & Leistungen von BOLZ INTEC GmbH auf Ihrem Markt, in Ihrer Branche und bei Ihren Kunden an.
Your questions, our answers
Through strict quality controls, ongoing research and development and compliance with all relevant industry standards and certifications, we ensure that every product meets the highest safety and quality requirements.
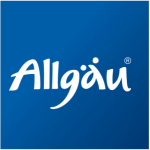
Do you have questions or are you looking for advice?
Simply book a 30-minute initial consultation with us via Calendly.